Jackshaft, also known as a countershaft, is an intermediate shaft/pole commonly found in motor vehicles, that sits between two rotating components, usually gears, and helps transmit the power between them. It is mainly used for synchronization or transfer of rotational force. Jackshafts have been in use for over a century, starting with simple mechanisms dating back to 1880s and have been part of many drivetrains as well as other industrial appliances. One of the first uses of the term jackshaft in the context of railroad equipment was in an 1890 patent application by Samuel Mower. In his electric-motor driven railroad truck, the motor was geared to a jackshaft mounted between the side frames. Alongside ICE (Internal Combustion Engine) vehicles, like cars (ex. Lotus Seven sports car series) and motorbikes (ex. Confederate P51 Combat Fighter), jackshafts can be seen in motorized bicycles (ex. Whizzer Motorbike model Pacemaker) popular in the 20th century, industrial conveyor belts and other industrial machinery.
Jackshafts in EVs
Vehicles, that run with combustion engines or ICEs rely on a jackshaft to efficiently distribute the produced power or simply optimise the conversion of energy to the wheels of the vehicle. ICEs cannot automatically regulate the speed of their rotation. In order to control it, different gears are introduced, to be able to increase and decrease the torque. If the jackshaft is part of a transmission system, it may have multiple gears or pulleys of different sizes attached to it. These gears or pulleys can have different ratios, allowing for torque conversion or speed adjustment.
Gear ratio can be calculated via the formula below:
(Gear ratio = # of teeth on the gear attached to the motor / # of teeth on the gear on the receiving end of the chain)
Pros:
- Flexibility of gear ratios:
Since all motors work best at a particular rotation speed, be it ICEs or EVs, adjusting the gear ratio will help the drivetrain match the motor's optimal operating range to the desired vehicle speed. Especially important in urban environments, where higher speeds are off limits. Additionally, by adjusting the gear ratios or pulley sizes allows for the conversion of kinetic energy during deceleration into electrical energy to recharge the battery, called regenerative braking. By adjusting the size or position of the pulleys, you can vary the speed at which the motor rotates, consequently controlling the energy production.
In our newest model, the motor used spins at a 6000 rpm. To synchronise the wheels with the initial spin, the gear ratio was made to be 6:1 with the help of a jackshaft, which makes it the optimal ratio that enhances and put the bike’s performance onto a new level.
- Space Optimization:
In certain cases, the electric motor may not be located directly in line with the rear wheel, thereby causing chain tension issues as the swingarm moves through its arc. A jackshaft can be used as an intermediary step to transfer rotational motion from the motor to the wheels in a more natural path, allowing for more flexibility in motor placement within the vehicle chassis or drivetrain assembly. With the motor placed in a more "out of the way" area, it allows our newest platform to easily fit in 6 - 10kWh into the platform. Moreover, in some cases, introduction of a jackshaft helps eliminate design complications. It can be placed right over or under the motor, without needing to redesign or reposition any obscuring mechanical and electrical parts. Such can be seen in the photo below:
New Paragraph
Cons:
- Loss of energy:
Any component in a drivetrain introduces energy losses due to friction and other mechanical inefficiencies. The introduction of a jackshaft can contribute to these losses, which can range from 1% to 5% of the overall power usage, reducing overall drivetrain efficiency and potentially impacting the vehicle's range and energy consumption.
- Additional weight:
Though arguably insignificant, a jackshaft adds a few hundred grams of mass to the overall weight of the vehicle. This is rather negligible in electric cars but is noticeable in electric bikes. This can impact the vehicle’s centre of mass and manoeuvrability.
- Complexity:
Introduction of multiple belts/chains and the jackshaft parts into a drivetrain slightly increases the overall maintenance cost, potential points of failure, and complexity of the whole mechanism.
In conclusion, implementation of a jackshaft in an electric vehicle opens many new possibilities for optimisation and control over the electrical motor itself, and maximizes battery space and therefore range, which is arguabily the most important factor when it comes to electric motorcycles.
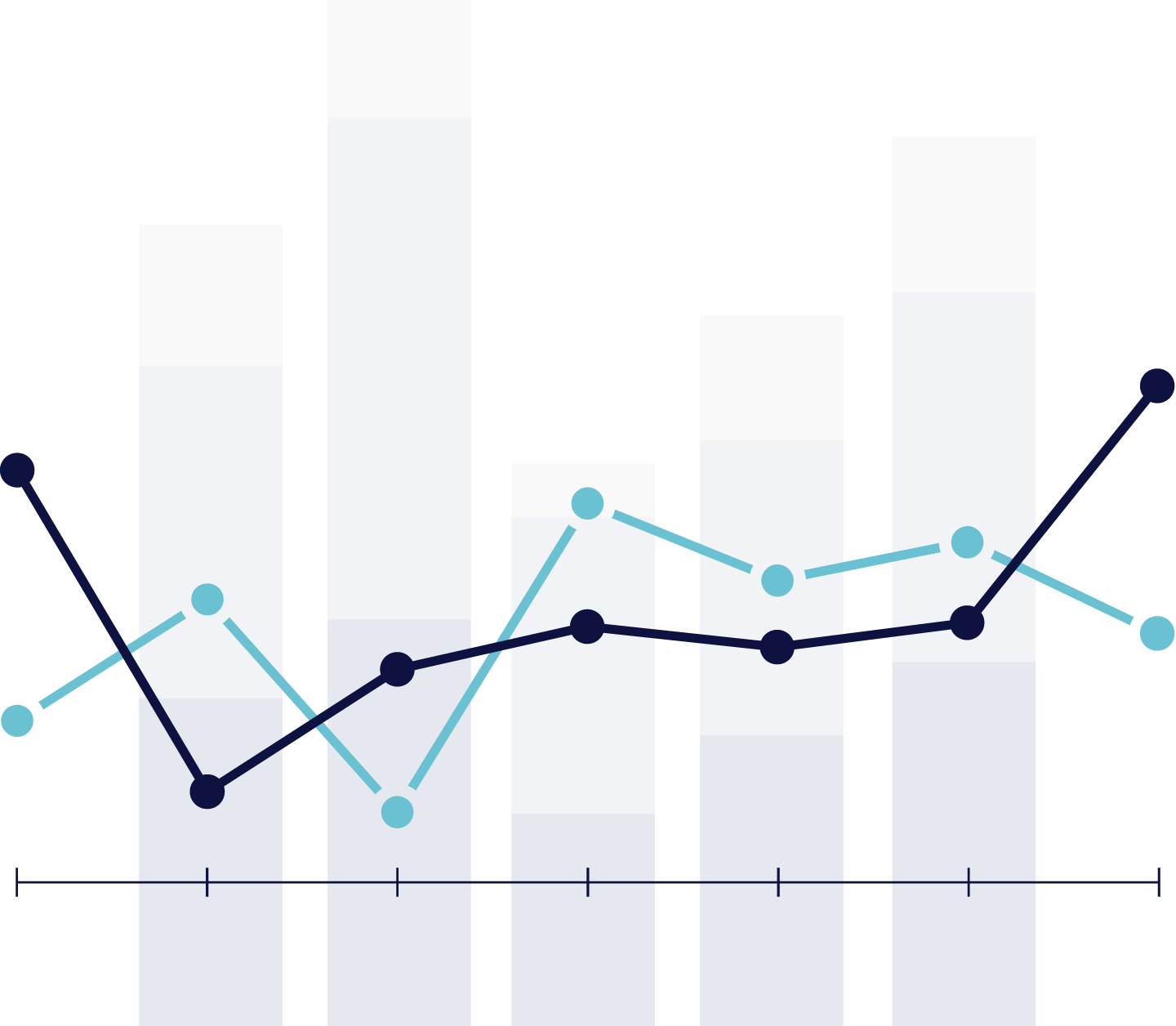
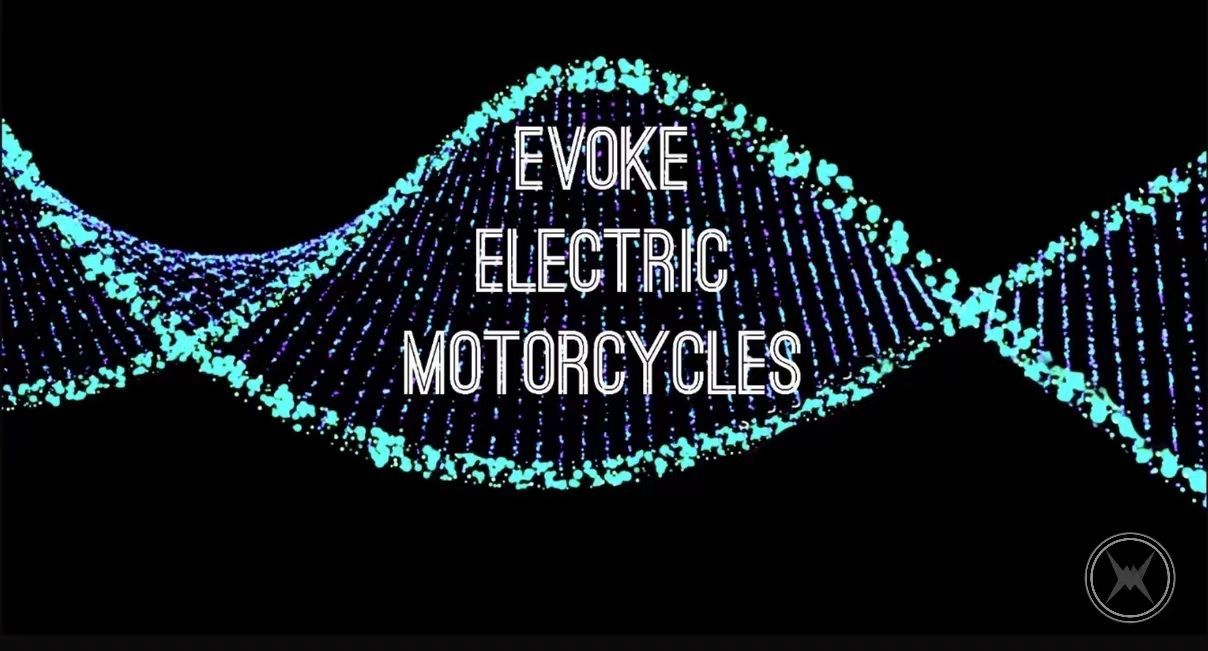